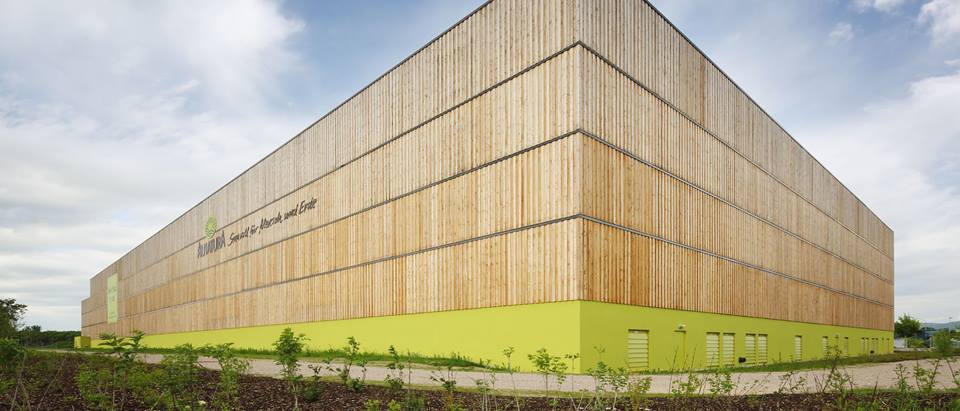
Auf großer Reise: Das Alnatura Verteilzentrum in Lorsch
Das Alnatura Verteilzentrum in Zahlen
- Rund 4.000 Paletten werden pro Tag im VZ Lorsch ein- und ausgelagert, das entspricht 135 bis 155 LKWs pro Tag
- 170 verschiedene Herstellerpartner aus Deutschland (80 %) und Europa (20 %) beliefern das VZ.
- Gesamtstellplätze Halle 15.000, Hochregallager 32.000
- Über 300.000 Kartons werden pro Woche in die Märkte geliefert
Das Rolltor am Wareneingang rattert nach oben. Wir blicken in den dunklen Bauch eines LKW und sehen rot – genauer gesagt, eine Menge roter Glasflaschen mit Tomaten-Passata aus Italien. Es ist 9:30 Uhr und damit mitten in der Warenannahmephase im Alnatura Verteilzentrum (VZ) in Lorsch. Die Ware vor uns hat bereits einen weiten Weg hinter sich. Auf Güterzügen ist sie von Italien bis Mannheim gereist, die kurze Strecke bis Lorsch dann mit dem LKW. "Gerade bekommen wir viel Ware aus dem Süden", erklärt Svenja Schaller, fachliche Assistenz Bereichsverantwortlicher Logistik bei Alnatura. "Tomaten werden nur einmal im Jahr in Italien geerntet, feldfrisch verarbeitet und dann hierher geliefert. Es gibt dann einen bestimmten Zeitraum im Jahr, in dem die italienischen Tomatenprodukte geballt hier ankommen."
Neben den Leckereien aus Italien finden alle Produkte des sogenannten Trockensortiments im Alnatura Verteilzentrum Platz, das heißt, Ware, die zwischen 12 und 22 Grad gelagert werden kann: beispielsweise Säfte, Müsliriegel, süßes und salziges Gebäck, Babygläschen und vieles mehr. Der Komplex besteht aus einer Lagerhalle in der Größe von 20.000 Quadratmetern und dem 2014 in Betrieb genommenen weltweit größten Hochregallager aus Holz. Eine ganze Menge Raum für Bio also. Svenja Schaller verdeutlicht das Ganze in Zahlen: "Würden wir zum Beispiel alle Stellplätze – insgesamt 50.000 – mit Müsliriegeln belegen (1.584 Stück pro Palette), dann hätten hier 79.200.000 Müsliriegel Platz!"
Wir begleiten unsere Passata-Palette noch ein Stück. Ein Mitarbeiter des Alnatura Logistik Partners "Müller – Die lila Logistik" scannt die Identifikationsnummer ein und gleicht alle Daten ab. Um die Abläufe im Verteilzentrum bestmöglich zu steuern, arbeitet Alnatura mit einem versierten Logistik-Dienstleister zusammen, der die Prozesse vor Ort verantwortet. Auch aus Gründen der Rückverfolgbarkeit sind reibungslose Abläufe von großer Bedeutung – muss beispielsweise einmal eine Warenherausnahme erfolgen, hat ein fehlerfrei geführtes Lagerverwaltungssystem immense Vorteile und dient als Basis für die Qualitätssicherung.
Darum schaut sich der Mitarbeiter am Wareneingang jetzt auch alles noch einmal genau an. Er prüft Daten wie das Mindesthaltbarkeitsdatum, begutachtet die umwickelte Folie und das Holz der Palette. "Die sensible Lichtschrankentechnik kann abstehende Folie beispielsweise nicht von einem Klotz unterscheiden, sodass die Palette in einem solchen Fall erst mal aussortiert wird", erklärt Thomas Flacker von Alnatura und verantwortlich für den Dienstleister. Nur wenn alle Faktoren stimmen, kann die Weiterverarbeitung durch Maschinen und Förderbänder sowie die Einlagerung problemlos erfolgen.
Sind die Bio-Produkte dann erst einmal drin, warten sie darauf, das Lager wieder verlassen zu dürfen. Je nach Produktgruppe dauert das im Schnitt 15 Tage. Manche Produkte sind nach 4 Tagen wieder "draußen", andere nach 30 Tagen. Ist die Bestellung einer Filiale im Verteilzentrum eingegangen, geht es an die Kommissionierung, also die Zusammenstellung der Produkte für die Filialpaletten. Das Packen ist eine Kunst und wird augenzwinkernd unter dem Begriff "Paletten-Tetris" geführt, wie Svenja Schaller lächelnd erzählt. Dafür sausen die Mitarbeiter in der Kommissionierung mit ihren Kommissionierfahrzeugen durch die Halle. Jeder Weg, jeder Handgriff sitzt.
Auf einer Palette tummeln sich im Schnitt 135 Kartons. Mit 1,65 bis 1,70 Metern Höhe und bis zu 800 Kilogramm macht sie fertig gepackt einen imposanten Eindruck. Schon während des Packens nehmen die Kollegen im Verteilzentrum Rücksicht auf die Gestaltung der Filialen. "Wir versuchen, den Aufwand für die Kollegen in der Filiale so gering wie möglich zu halten. Wenn die Nudeln dort neben der Tomatensauce stehen, dann versuchen wir das beim Packen zu berücksichtigen, damit sie in der Filiale nicht Zickzack laufen müssen", erklärt Svenja Schaller diesen Ansatz.
Gefüllt mit einem bunten Produktmix werden die fertigen Paletten dann an der Warenausgabe von LKWs abgeholt. "Hier achten wir aus Gründen der Nachhaltigkeit darauf, so oft wie möglich "Full-Truck-Loads" zu haben", sagt Thomas Flacker. Das bedeutet, dass ein LKW immer voll fährt. Und ein Fahrzeug, das Ware vom Hersteller anliefert, fährt im besten Fall um das Gebäude herum und nimmt am Warenausgang wieder Ware für die Filialen mit – das sind die sogenannten Rundläufer. "Auf deutschen Straßen fährt fast jeder fünfte LKW leer, da möchten wir gegensteuern", so der 34-Jährige.
Vom Verteilzentrum aus liefern die LKWs die Bio-Produkte direkt in die Filialen, die sich im Umkreis von 200 Kilometern befinden. Die restliche Ware wird an regionale Bio-Großhändler verteilt. Dort findet das sogenannte "Cross-Docking" statt: Die Paletten werden zusammen mit den Tiefkühl- und Molkereiprodukten, Obst und Gemüse, Fleisch, Backwaren sowie Drogerieprodukten gebündelt an die Alnatura Filialen im Umland geschickt. "Häufig ist es aber auch so, dass Produkte wie frisches Obst und Gemüse von den lokalen Bauern direkt ausgeliefert werden", sagt Svenja Schaller. "Auch die Backwaren kommen meist frisch vom Bäcker in die Filiale, darum bekommen die Kunden auch in Hamburg andere Brötchen als in Mannheim", ergänzt Thomas Flacker.